OIL DIVISION
REFINING PROCESS:
- Currently in Ragasa, we have the most advanced Oil Refining technology, which is an important competitive advantage.
- There are production lines with more than 20,000 cartons per day.
- The refining process begins with the Crude Oil produced by the operation of the mills.
- The refining of crude oil is a process that chemically neutralizes vegetable oils and fats.
- Neutralizing means removing most of the free fatty acids (FFA) and non-hydratable phospholipids from the oil.
- Phospholipids are fats in which a fatty acid has been replaced by phosphorus and a nitrogen compound.
- The Refining process is also known as RBD and consists of 4 stages:
- Refining (Neutralization)
- Purification
- Bleached
- Deodorized
Each stage of the process removes different impurities to produce the oil of optimum quality.
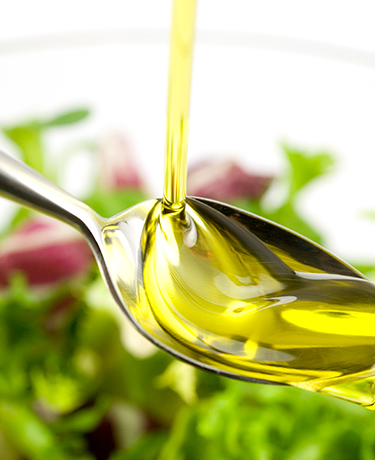
Gums residues that may have the crude oil, as well as other unwanted compounds are eliminated, which, if not removed, degrade (make it rancid) very soon the oil.
Reduction of the content of metal compounds, which affect stability, is complete.
The oil is discolored by removing compounds that affect the hue (color) of the oil. The chlorophyll content of the oil is reduced.
Odor and taste are removed from the oil, so it is neutral.
So once the crude oil passes through the RBD process it is transformed into refined oil, finished oil, which is pumped to storage tanks that have a nitrogen atmosphere to prevent the entry of air that affects the oil.
Each storage tank has a multiple manifold of four valves that allow to take oil of a desired level, which is pumped to the tanks of the transports that send the product to the client.
PACKAGING PROCESS:
Refined Oil that meets the strict specifications of brand quality, goes through the packaging process.
The packaging process consists of seven stages which are:
- Injection
- Blown
- Fill
- Labeled
- Packing
- Palletizing
- Storage
It consists of melting resin (PET) and placing it in a mold, where after obtaining the form is cooled to finally obtain the preform. This is transferred to a feeder and later to the machine blower where the bottle is obtained. We use only polyester resin (PET) to inject the preforms.
Through compressed air of high pressure and with the use of molds specific for each type of bottle the PET bottle is obtained in its final form.
The bottles pass to the filling machine which has two types of control for filling, by weight or by volume.
Once the bottle is filled, liquid nitrogen is dosed to remove the residual air and to avoid the oxidation of the oil. Immediately proceed to place the cap.
Once filled the bottle is labeled. We have two types of labeling, one envelope with Hot rubber and another called “Spot”, with cold rubber.
When leaving the label the bottle is coded with an ink printer. The Lot and the Preferential Consumption Date are registered, which is 14 months.
The packaging system consists of a box setter, a boxer, a box closer, and a bottle content checkweigher.
The palletized system allows us, manually or automatically, to form pallets of different quantities, for different customer requirements.
The boxes pass to the Finished Product Warehouse from where they are shipped.